The layered pink walls of Foster + Partners' Narbo Via bring the rustic charm of the southern French soil to precision-engineered concrete, writes Tony Whitehead.
Exposed concrete has become a popular choice for designers of prestige museums and galleries: from the spectacular V&A at Dundee, to the equally striking Glassell School of Art in Texas, architects have deployed both in-situ and precast concrete to create buildings that are highly distinctive from the outside, yet appropriately quiet and relaxed once you step inside.
The same can certainly be said of Narbo Via, a new museum of antiquities in the port city of Narbonne in southern France. But this building – not unusually for a Foster + Partners design – has something a little bit different: its massive walls are made from terracotta stripes of rammed concrete.
Made by compressing an almost-dry mix, rammed concrete is still a rare sight anywhere, and tends to feature more in designer homes than civic projects. So how did it come to be used on a major cultural building spanning nearly 9,000m2? “We originally envisaged a structure clad in precast concrete,” says architect Hugh Stewart, a partner at Fosters. “But as the design developed, we began to favour a more monolithic approach, and there was a strong desire within the office that if it looked monolithic, then it should be monolithic.
We considered conventional in-situ walls with insulation in the middle, but then decided we were after something more textured, more gritty, a bit more of the place. We looked all over the world for something that could provide that, before deciding on rammed concrete.” The chosen wall system was a Canadian product called Sirewall – “Sire” standing for “structural insulated rammed earth”.
Although there is some debate about where rammed earth finishes and rammed concrete begins, its sand, aggregate and cement mix would seem, despite its name, to make Sirewall more at the rammed concrete end of the spectrum. However you describe it, the walls at Narbo Via are impressive not only aesthetically but also in terms of how hard they work for the building: their many functions include structure, weather shield, internal finish, acoustic control, thermal “flywheel” and humidity regulation.
In Roman times Narbonne was a major port, and Narbo Via is constructed primarily to house a collection of more than 1,000 Roman funerary stones recovered from the city’s medieval walls in the 19th century. These are displayed on a long wall of metal shelving that cuts the 8,765m2 museum’s rectilinear plan into two squares. One is dedicated to double-height public galleries; the other, featuring a mezzanine floor, provides space for education, research, restoration and administration. The site is prone to flooding, so the whole building is raised on a low, landscaped podium – lending some elevations an appropriately classical or temple-like appearance. Voids below the ground floor in-situ concrete slab have been used to house the majority of primary services.
But it is the walls which catch the eye and define the building. “It’s worth noting that these are structural walls,” says Foster + Partners head of structural engineering, Roger Ridsdill Smith. “They have to resist the vertical loads of a precast-concrete roof structure, as well as lateral loads including wind, and there is also seismic loading to consider. So we needed substantial and dependable structural properties from the walls – not least for them to be acceptable in the context of stringent French codes.” To achieve all of the above, the 6m-high walls are 800mm thick, comprising a 200mm outer skin, 200mm of solid foam insulation, and a 400mm inner skin.
The rammed concrete system used at Narbo Via was developed by Vancouverbased Sirewall, a company founded in 1992 by self-styled “legendary dirt Jedi” Meror Krayenhoff. So how does it work? “Soils and aggregates are different all over the world,” says Krayenhoff. “Our technology is able to analyse what’s available and come up with an optimal mix design.
A big difference between Sirewall and most plain rammed earth systems is the strength. They don’t tend to get much beyond 7.5MPa, whereas we achieve a minimum of 20MPa and Narbo Via was 30MPa. You can blast Sirewall with a pressure washer and it will just stay there.”
He explains that a typical Sirewall mix will have 9% ordinary cement and just 8% water, or something like half that of a standard concrete mix. Sirewall also contains a hydrophobic admixture which, together with the compacted density of the wall, prevents air and water ingress.
This means there is no need for expensive corrosion-resistant stainless steel rebar, as required by some rammed earth systems. “There’s a big difference in aggregate too,” says Krayenhoff. “Concrete tends to have, say, a 20mm aggregate and a 600 micron sand, but we use the full range in between, depending partly on the granularity of the finish required. Although we can’t have organics in the mix – we don’t just stick a shovel into the nearest bit of countryside – we can have up to 10% silt and 15% clay, again very different to standard concrete.”
He says that the wider range of particle sizes has a crucial influence on the way the mix constituents bond under pressure from tamping. “What we are doing is getting it all to fit together tightly – effectively creating engineered sandstone, but a little quicker than geological processes." Compressing many different sizes of particle together means there is less space between the particles than between sand and aggregate in standard concrete: “It’s one reason we are able to use less cement – because there’s less of it that’s effectively just being used as filler.”
In addition to reduced cement and water content, Kreyanhoff claims other environmental benefits for his product: “We can use local products, reducing transport. We can use manufactured rather than scarcer natural sand, and we have also used recyclate or waste products in our mixes. And what you end up with has all the thermal mass benefits of exposed concrete, but as well as a thermal flywheel, you get a humidity flywheel.
Sirewall absorbs excess humidity, and releases moisture when the air is dry.” Sirewall’s customers also appreciate its acoustic properties: “We did a house for Randy Bachman of the rock group Bachman Turner Overdrive. He had one room with very smooth walls for echoey reverb, and another with a more granular finish for a sound softening effect.”
The system does have limits: it is difficult to tamp if the space above the “pour” is not clear. Nor can rammed concrete flow into quite the small detail that concrete, particularly self-compacting concrete, might be able to. Some detail is possible though, as evidenced at Narbo Via by the creation of a relief map of the Roman Empire on the rammed concrete wall.
Kreyanhoff also concedes that rammed concrete is labour-intensive: “Some yearsback we compared bespoke house-build costs in North America and found a Sirewall equivalent might cost 15% more – which obviously we think is well worth it."
“The inner and outer skins of rammed concrete are joined by horizontal rebar which connects vertical rebar in each skin,” explains Ridsdill Smith. “But we didn’t want tie holes, so the forms are just pushed up to the wall and held in place without them. There’s less need for ties because, being created in layers, the drier mix does not exert hydrostatic pressure in the way that wet concrete would” (see box).
The attractive striations result partly from the rammed concrete construction process in which a 200mm-deep layer, usually some 6m long, is “poured” into forms (although the mix, Stewart says, is “dry in the hands”). It is then compressed by hand-held mechanical tampers. After this it is firm enough for forms to be removed if desired, though the concrete continues to cure, with a strength gain curve to 28 days somewhat steeper than many concretes.
As for the unusual colouring, the aggregates are from a local quarry, but Stewart says that the shades and patterning mainly result from alternating mixes with various amounts of oxide colourants. “We created two palettes – one more blood red and this one, which is more pink and orange. After trials, we decided the first was too strong but the second was similar to the local terracotta roof tiles, helping the building to be of its place.” As with most larger Sirewall projects, the Narbo Via site used a volumetric mixer customised to work with the drier mix. Once the mixer had been calibrated, the colour could easily be changed from one lift to the next, allowing each layer to be visually contrasted. “The arrangement of differing hades is carefully chosen,” explains Stewart.
“We had full-size paper prints hanging in the office, testing out the shades and helping us decide exactly what the order should be. It’s meant to look natural, but it’s not the slightest bit random.” A number of environmental benefits result from the wall design.
The 400mm inner layer, exposed to the air inside, absorbs and releases heat to even out diurnal temperature variations and saves energy by reducing the need for heating or cooling. There is so much exposed thermal mass – the roof is also exposed concrete – that the benefits extend beyond daily cycles to seasonal ones, says Stewart. “It is a happy marriage between looking beautiful and having a significant thermal flywheel effect. The inside stays remarkably cool, even on the very hot days this part of France enjoys in summer.”
Material usage is reduced as there is no separate external cladding or interior lining required. “All the materials are basic and local to the site, reducing the environmental costs associated with manufacturing and transport.” Aesthetically, Stewart is pleased with the way the walls’ gritty appearance contrasts with both the floor and ceiling of Narbo Via. The internal floor is a polished concrete floating screed cast on rigid insulation over structural hollow core slabs, “with a bit of quartz magic dust thrown over it to make it sparkle”. The exposed roof structure is also smooth, being precision-made from precast concrete.
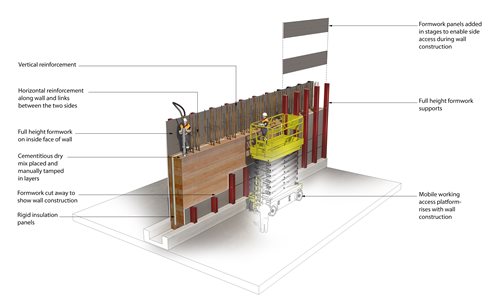
Insulation is positioned in 600mm-tall boards and the mix poured in 200mm-deep layers either side. Operatives can then stand astride the insulation to tamp.
When the rammed concrete reaches close to the top of the insulation board, horizontal rebar connecting the reinforcement in the outer and inner skins can be ground into the top edge of the insulation, before further insulation board is added and the process repeated.
The technique results in a small amount of cold bridging through the rebar, though this is rendered negligible by the thickness of both the insulation and the concrete skins.
In a less distinctive building, this roof structure might qualify as the main design event, cantilevering out from the walls on all sides. The walls are spanned primarily by seven massive precast concrete beams, H-shaped in section and 1.4m high. “We wanted an exposed and servicefree ceiling,” says Ridsdill Smith, “so having H-sections allowed us to use the 200mm cavity for service distribution, and also for insulation where this was needed at the building perimeter.” Like most of the precast concrete in the building, the beams were manufactured by Girona-based Planas, each one made in several sections. Planas project manager Lluc Valldosera explains: “Some of the shorter primary beam sections were fabricated with an H-shaped mould, but the larger ones were fabricated in two units and assembled on site.
The largest individual beam was 21m long and weighed 22 tonnes, so the full beam with the two pieces assembled weighed 44 tonnes. There were seven of these, plus another seven 18m long, and another 35 smaller units of 12m.” All the units were made from steel moulds, and the mix contained 1% white oxide to achieve the paler shade required. The secondary beams run at right angles to the tall H-beams and span up to 15m between them.
These are made from 165 inverted U shaped sections, typically 15m long, 1.75m wide and 1m high. Spanning between the “U” section beams are 470 reinforced concrete planks, the majority 7.5m long, 1.35m wide and 60mm thick. “We worked with Planas to design a slight taper into both the primary and secondary beam units to ensure easy striking and a smooth finish,” says Ridsdill Smith. “The roof is finished with a structural concrete screed poured on top of the precast planks. The lateral loads, due primarily to seismic forces, descend from the roof, through the primary beams and into the walls via reinforced cast in-situ connections.”
The genius of the Narbo Via design is in no small part down to how this massive, highly visible roof structure works with the similarly substantial and distinctive rammed concrete walls. The low, long proportions of the building conspire to make these vast elements look elegant, as well as reassuringly solid and built to last. The Romans would surely approve.